Laser cutting machine is an advanced plate processing equipment in the industry.
In the actual production process, the cutting method directly determines the production efficiency and workpiece quality.
Therefore, it is necessary to explore effective cutting skills in order to improve production efficiency and product quality and reduce the waste rate of plates.
This post mainly describes several cutting techniques that have been fully verified in the production process, including the application of frog leaping empty stroke feed, centralized perforation, micro connection, and the optimization of perforation point in laser cutting.
In the actual production, the cutting quality and processing efficiency of the workpiece are effectively improved through the above methods.
Working Principle Of Laser Cutting
Laser cutting is a kind of non-contact processing with high energy density and good controllability. It uses the laser beam emitted from the laser generator to focus the laser beam into a spot with a minimum diameter of less than 0.1 mm through the optical path system, so as to achieve high power density laser beam irradiation conditions. After the heat of the laser is absorbed by the irradiated workpiece material, the workpiece temperature rises sharply and reaches the melting point. The material begins to liquefy and form holes, and with the high-pressure air flow, with the relative position of the beam and the workpiece moving, the material finally forms a continuous slit.
In order to accelerate the melting of the material, blow away the slag and protect the cutting seam from oxidation, it is necessary to add auxiliary gas suitable for the material to be cut, so as to achieve excellent cutting speed and cutting quality.
At present, the common cutting methods mainly include straight cutting, wire cutting, profiling cutting, flame cutting, water jet cutting, laser cutting and so on.
Among them, laser cutting is more and more widely used in steel plates under 16mm because of its smooth incision, accurate size, high speed, low noise, less dust and the ability to cut various complex shapes.
In the actual laser cutting process, cutting skills are very important.
Therefore, mastering all kinds of laser cutting skills is the key to improve production efficiency.
Through experimental exploration, we summarize the following several laser cutting techniques will be used. Through the application in the actual production, the production efficiency is effectively improved and the waste of materials is reduced.
Frog Leaping Empty Stroke Feed
Frog leaping is an idle running of the laser cutting machine.
As shown in Figure 1, after hole 1 is cut, hole 2 is cut. At this time, the cutting head should move from point A to point B. Of course, turn off the laser during the movement. The movement process from point A to point B is called “idle running”.
The general idle stroke of the laser cutting machine is shown in Figure 2. The cutting head has to complete three actions: rising (to a safe enough height), translation (to the top of point B) and falling.
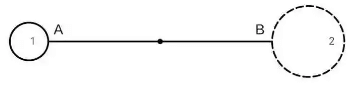
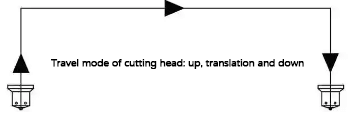
The efficiency of the equipment can be obviously improved by compressing the air travel time.
If the three actions completed in order are changed into “simultaneous”, the idle time can be shortened, that is, when the cutting head moves from point A to point B, it will rise at the same time; As it approaches point B, it descends at the same time, just like the frog jump, as shown in Figure 3.
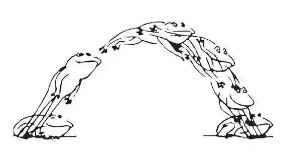
With this method, only the translation time from point A to point B is occupied, and the rising and falling time is saved.
The laser cutting machine adopts frog leaping idle stroke feeding, which effectively reduces the idle stroke movement time and improves the processing efficiency.
Concentrated Perforation
Centralized perforation, also known as pre perforation, is actually a kind of processing technology, which is not available in general laser cutting equipment.
For example, when laser cutting thick plate, each contour of the cutting process has to go through two stages of perforation and cutting.
The conventional process is perforation → cutting profile 1 → perforation → cutting profile 2, as shown in Figure 4.
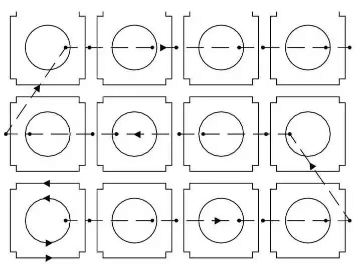
The small dot is the perforation point, and the arrow is the cutting path sequence.
The so-called centralized perforation is to execute all the perforation processes on the whole sheet in advance, and then execute the cutting process, as shown in Figure 5.
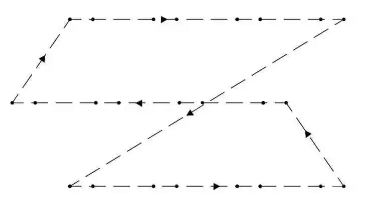
The small dot in the figure is the perforation point, and the arrow is the order of the idle travel path.
The process route of centralized perforation is to complete the perforation of all contours, return to the starting point and cut all contours.
Compared with conventional processing technology, the total length of the running track of the equipment is increased, but the advantage is that the centralized perforation can effectively avoid overburning.
Especially in the process of thick plate perforation, heat accumulation is formed around the perforation point. If it is cut immediately, overburning will occur (Fig. 6).
The centralized perforation process is adopted to complete all the perforation, return to the starting point and then cut. Due to sufficient time for heat dissipation, the over-burning phenomenon is avoided.
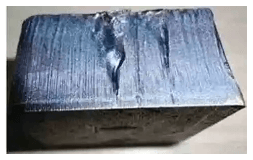
Application Of Micro Connection
During laser cutting, the sheet metal is held by the serrated support bar. If the cut parts are not small enough, they cannot fall from the gap of the support bar;
If it is not big enough, it can not be supported by the support bar, then it may lose its balance and the workpiece may be warped.
The cutting head with high-speed movement may collide with it, which may cause shutdown or damage, as shown in Figure 7.
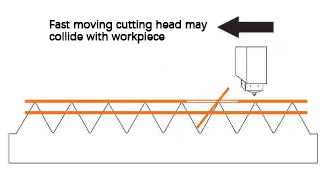
However, this kind of problem can be avoided by using micro connection cutting technology.
The specific method is as follows: when programming the laser cutting of the figure, the closed contour is intentionally broken at several places, so that after the cutting, the parts and the surrounding materials will stick together and will not fall, and these broken places are called micro connections (Fig. 8).
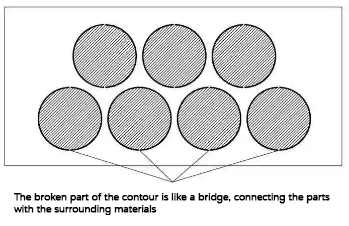
The disconnection distance is about 0.2 ~ 1 mm, which should be selected according to the principle that the disconnection distance is inversely proportional to the sheet thickness.
In the process of laser cutting, when the micro connection is used to connect the parts with the surrounding materials, the appropriate number of micro connections should be added according to the length of the contour;
It is also necessary to distinguish the inner and outer contours, so that the inner contour (scrap) without micro connection is dropped, while the outer contour (workpiece) with micro connection is adhered to the base metal, thus eliminating the sorting work.
Analysis Of Deformation Of Small Hole (diameter Less Than Plate Thickness)
In general, the size of the cutting hole is specified as follows:
(1) When cutting carbon steel plate within 8mm, the hole diameter shall not be less than the thickness of the plate.
(2) When cutting carbon steel plates within 10 mm, the hole diameter shall not be less than 1.2 times of the plate thickness.
(3) When cutting stainless steel plate within 4mm, the hole diameter shall not be less than the thickness of the plate.
(4) When cutting stainless steel plate more than 4mm, the hole diameter shall not be less than 1.2 times of plate thickness.
However, in laser cutting production, we often encounter the workpiece whose aperture is less than the thickness of the plate, and it is difficult to process and the cutting quality is poor.
The main reason is that when the program cuts the circular hole whose diameter is less than the thickness of the plate, the default cutting mode of the machine tool changes from the original continuous cutting to the pulse perforation cutting, which makes the laser energy too concentrated in a small area, and the non machining area is also burned, causing the hole deformation and affecting the processing quality.
After our company’s exploration and attempt, we found that if we use melting cutting instead of flame cutting, that is, when the program runs to cut small round holes, we should adjust the cutting state, use high-pressure nitrogen instead of oxygen for cutting, and then change back to oxygen cutting when the small holes are cut.
The small holes cut by this method are very regular in both sides, which can meet the requirements of qualification, reduce the reject rate and improve the production efficiency.
Selection Of Piercing Point In Laser Cutting
In the process of laser cutting, after the laser beam continuously irradiates on the material, a pit is formed in the center, and then the airflow coaxial with the laser beam will quickly remove the molten material and form a small hole.
This hole is similar to the threading hole in WEDM. The laser beam takes this hole as the starting point for contour cutting. Generally, the line direction of the laser beam in the flying light path is perpendicular to the tangent direction of the cutting contour of the machined part.
Therefore, there will be a great change in the cutting direction from the time when the laser beam starts to penetrate the steel plate to the time when the laser beam enters the contour cutting.
From the tangent direction perpendicular to the cutting contour to coincide with the tangent of the cutting contour, that is, the included angle with the tangent of the contour is 0 °, this will leave a rough cutting surface on the cutting section of the processed material.
The main reason is that the direction of the laser beam changes too fast in a short time.
Therefore, we must pay attention to this problem when using laser cutting parts.
Generally speaking, when the workpiece has no roughness requirements for the surface cutting fracture, the manual processing can be avoided in the laser cutting programming, so that the control software can automatically generate the perforation points;
If the cutting section of the workpiece to be processed has higher requirements, it is necessary to adjust the perforation. Usually, it is necessary to manually adjust the starting position of the laser beam when compiling the laser cutting program, that is, manually control the perforation point.
It is necessary to move the original perforation point generated by the laser program to the required reasonable position to meet the requirements of surface accuracy of machined parts.
As shown in Fig. 9, if the workpiece has the cutting surface roughness requirements for the arc part, when compiling the laser cutting program, the cutting start (perforation point) should be set at A and C, but not at B and D. If the workpiece only needs the roughness of the cutting surface of the straight edge, then when programming the laser cutting program, the starting point of cutting should be set at B and D, but not at A and C.
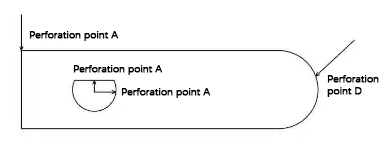
Similarly, as shown in Figure 10, if the shape design of the workpiece has accuracy requirements for the arc, when we compile the laser cutting program, the cutting starting point (perforation point) can only be set at D.
If this part only requires the accuracy of the straight-line edge, then we can select any point except D point when programming the laser cutting program.
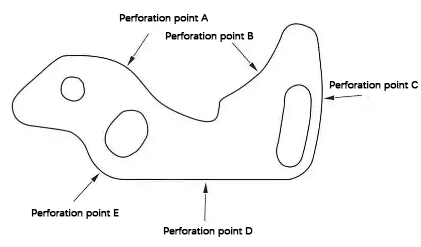
Conclusion
In the actual production process, the operation of laser cutting machine is complex and fine, with a variety of workpieces and materials
With the growing maturity of cutting technology, as long as we can skillfully use all kinds of cutting skills and accumulate experience in solving problems, we can improve the processing and production capacity of people and equipment.
Cr: machinemfg